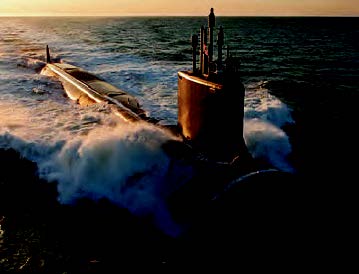
S2747— Automated Preheat Temperature Monitoring
Objective
Many facets of submarine construction involve controlled heating of materials during
welding processes to ensure the quality of welds. In submarine construction the rigid
monitoring and controlling of the temperatures during the welding processes are
highly manual processes. Workers continuously monitor the temperature of welded
sections, and adjust the heater controls to maintain the correct temperature profiles.
Weld preheat and post-welding heat treatment processes, which require manual
temperature monitoring, measurement, and documentation methods, use significant
amounts of labor.
This Electro-Optics Center (EOC) project follows a proven systems engineering
approach to develop an automated temperature monitoring and digital reporting
solution. The initial phase developed and optimized physical attachment method(s),
temperature correlation, and logistics in a relevant environment. The project is
defining the requirements for data processing and its integration with temperature
control systems. The results of the project will be a detailed technical report and
shipyard implementation plan for automated temperature monitoring in a shipyard
environment.
Payoff
There is presently a group of technicians who are responsible for manually monitoring
and documenting the temperatures for critical heating processes in the shipyard.
According to the shipyard, the time involved in manual temperature monitoring
is roughly 9,000 hours per year, or about $340K per VIRGINIA Class submarine
hull. The vision of this project is to automate the monitoring processes so that
these technicians can spend more time performing setup tasks and only address the
correction of out-of-limit processes. By having access to critical material temperature
data, a new level of temperature traceability could enhance weld issue diagnosis
capabilities in the future
Implementation
Because of the wide applicability of temperature monitoring scenarios and methods,
this project included specific tasks that drive commonality into implementation
of the methods. There is a large amount of cooperative work between EOC and
shipyard engineers to ensure the resulting functional system specification will be
implementable. Where development work is required at EOC laboratories, there is
an accompanying transition to a non-production task at the shipyard to assure that
personnel are current with the methods development. The knowledge gained during
the task, in conjunction with the resulting system specification document, will be the
recipe for a successful shipyard implementation.
Project Details
-
Period of Performance:
October 2018 to September 2020 -
Platform:
VCS / CLB Submarines -
Center of Excellence:
EOC -
Point of Contact:
Mr. David Ditto
(724) 295-7011
dhd10@arl.psu.edu -
Stakeholder:
PMS 450, PMS 397, PEO Subs -
Total MANTECH Investment:
$1,083,000